Sandoz
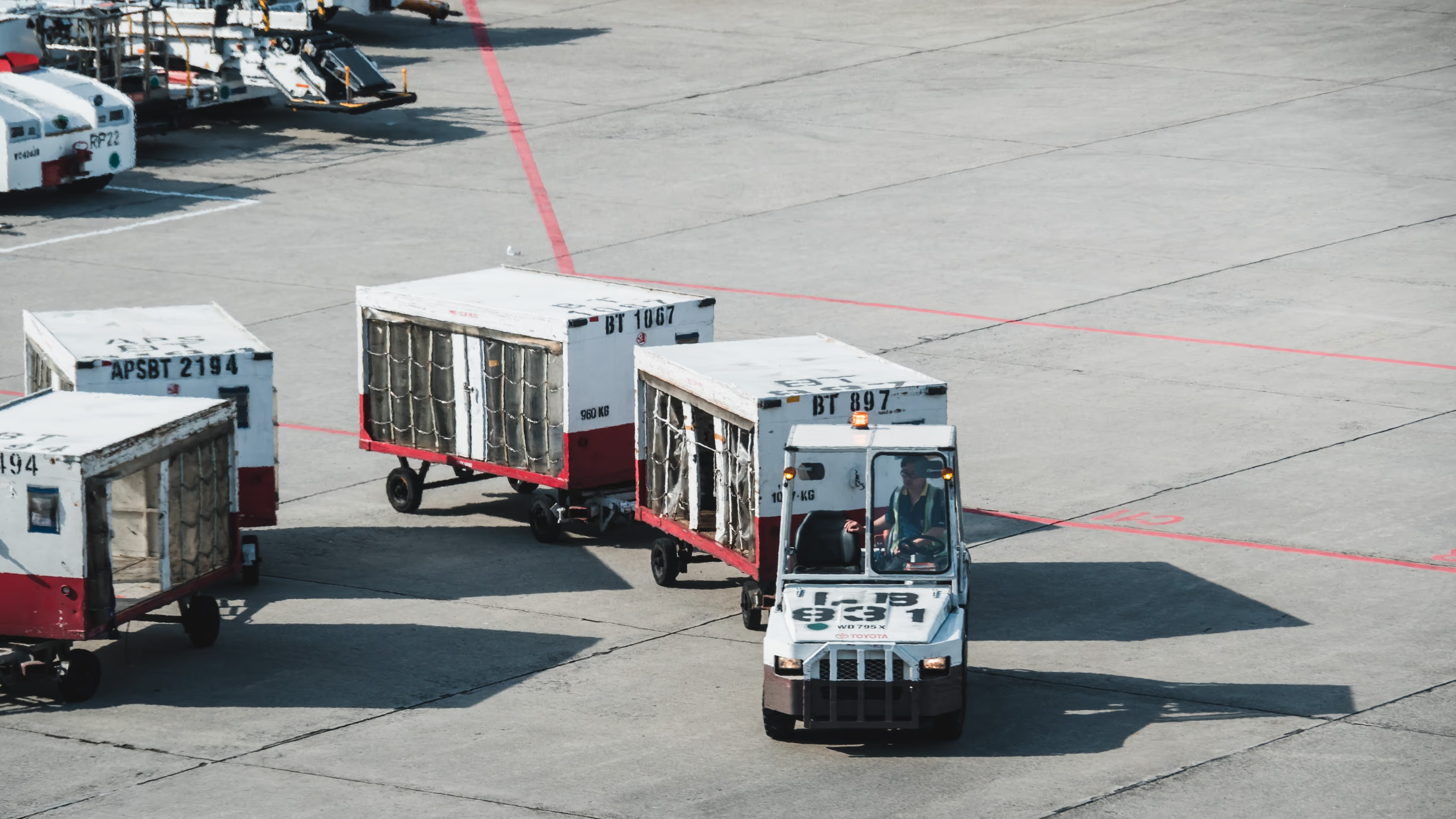
The safety and integrity of drug delivery on time and in full has never been more important than in Covid pandemic ridden world. In response to the dangers of getting lost, damaged, or stolen, TSS has together with Sandoz, a division of Novartis, a proven case history of tracking and ensuring the safety of pharmaceutical packages.
On time and in full, when it matters most
Effective and reliable monitoring of pharmaceutical shipments is a key factor in ensuring safe distribution, but recently it has become even more critical. COVID-19 has demanded an even greater sense of urgency and timely delivery - all at a time when logistics operators are experiencing an unprecedented level of strain in the system.
Sandoz, a division of Novartis, have been manufacturing the drug hydroxychloroquine (HCQ), which was seen to have potential for treating symptoms of COVID-19. Sandoz donated 110 million doses to WHO, to conduct global full-scale clinical studies across laboratories and hospitals. Managing supply chain logistics was to remain the responsibility of Sandoz, who identified the need for urgent support with surveillance of these critical shipments.
Real-Time Monitoring (RTM)
The real-time monitoring solutions offered by TSS include temperature loggers with GPS sensors, software with Geotracking functionality, and 24/7 services for surveillance and intervention if needed (Control Tower Services).
The timeline, as with so much relating to the pandemic, was unprecedented. The request was received on Tuesday 31st March 2020, with the initial shipments already scheduled for the following Tuesday. The objective was to monitor shipments from Switzerland for up to 100 global destinations and ensure safe delivery.
In the event of a shipment ending up “off route” TSS should help locate the shipments and engage local law enforcement to retrieve them. Given that this operation had to be carried out in a time of severe supply chain disruption, it was also critical to be able to accurately anticipate deliveries.
So, why was it so important for Sandoz’s to take the leap into real-time monitoring?
Firstly, the drug was considered to be at a high risk of theft and so the ability to use tracking to provide special protection was seen as a necessary investment. Secondly, the high-value nature of the drugs - both financially and medically, meant that it was vital that each shipment arrived at its destination in a perfect condition – particularly challenging considering the lack of direct flights available in the wake of COVID-19.
Actioning a solution
TSS are not the only provider of real-time monitoring available on the market, and Sandoz naturally explored numerous options regarding the project. However, based on TSS meeting their sense of urgency and the high quality of previous deliverables, Novartis trusted TSS with this important assignment.
Novartis Technical Operations conclusions stated that
“TSS’ software solution is flexible and reliable, and we have a strong existing business relationship. As such we can vouch for their reliability and professionalism, and we understand the capability of their technology solutions”.
“We chose TSS because they have proven to us in the past that they provide a good service. They are a supplier we can rely on”,
summarized Thomas Naef, Global Warehousing & Distribution Process Manager for Novartis Technical Operation.
Sandoz assigned three key organizational stakeholders to coordinate the project, representing quality, security, and logistics. The RTM solution was put in place within only five business days, building on the existing customer platform of TSS.
As Kai von Borck, Account Manager at TSS reflects:
“For this specific project we found real-time monitoring to be critical in identifying logistics challenges, allowing us to find alternative solutions in the face of any problems, and informing our client where any specific shipment was located at any time”.
He continues:
“Throughout the project, we have intervened a number of times to save time and assist on shipments in transit. For example, on shipments to El Salvador and Cincinnati we were to able contact the freight forwarder, directing them to alter the route and achieve earlier delivery”.
What’s next?
Real-time monitoring is currently being explored in many organizations, to support critical shipments of high-value goods. Undoubtedly, this is a trend that is certain to evolve along with technology, the industry, and consumer needs. This project, in particular, demonstrates not only the value of real-time monitoring, but also TSS’s unique flexibility and speed in deploying temperature management solutions that can cope with the most challenging of circumstances.