GlaxoSmithKline
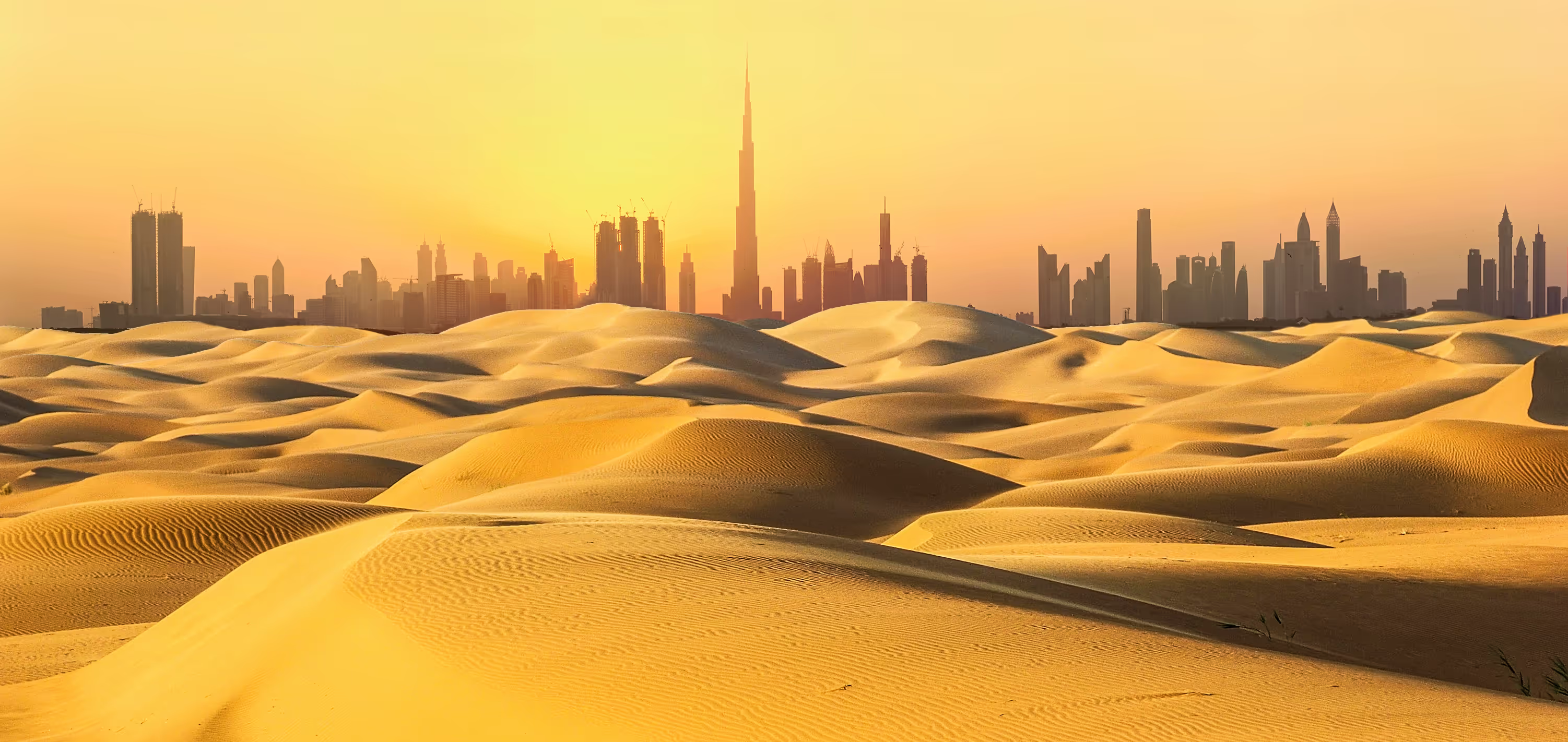
The Middle Eastern region often faces significant logistics challenges in transporting temperature-sensitive products. The climatic conditions, with high temperatures and humidity levels, can quickly compromise the integrity of the products during transportation and storage, particularly pharmaceutical drugs.
These challenges require advanced temperature-controlled logistics solutions that utilize state-of-the-art temperature control and monitoring technologies to ensure the safety and efficacy of pharmaceutical products throughout their supply chain. Despite these challenges, Dubai has become an important hub for secondary distribution of pharmaceuticals to the Middle Eastern, as well as theAsian regions.
The challenges of the supply chain advancements
In a region where urban expansion is extensive, operational advancements for many organizations need to accelerate quickly to adapt to shifting circumstances. For Mr. Ahmed Accoush, Distribution and Logistics Manager-Gulf, and his team at GSK in Dubai, these challenges are part of their daily work, and they are always in pursuit of optimizing procedures.
GSK works with the logistics company GAC in Dubai to manage secondary distribution in the region. Time is of the essence when handling delicate cargo, and the staff at GAC needs to balance efficiency with quality to meet their customers’ requirements.
“We manage up to 150 loggers per day in various shipments, apart from all other shipments departing the site. Every minute counts and we can’t spend too much time on manual administration,” said Mr. Aneesh Mattol, Senior Supervisor at GACLogistics in Dubai.
Every minute counts and we can’t spend too much time on manual administration.
However, automating manual processes in heavily controlled industries, such as pharmaceutical manufacturing and logistics, is complex. It is affected by global and local regulations, laws, and distribution practices and often involves several stakeholders.
Automating manual processes and digitizing documentation
Temperature control procedures vary, due to diverse user needs and circumstances. The technical prerequisites, shipments requirements and local procedures define the solution. GSK and GAC in Dubai were already using advanced technological systems (WMS and ERP) and had many years of experience in temperature management. To optimize the processes, they decided to automate manual processes through an integration between solutions from GSK, GAC and TSS.
GSK and GAC needed a flexible temperature monitoring solution, supporting shipments with varying temperature profiles without requiring complicated forecasts. Therefore, a small handheld and high-quality logger with a USB connection was the best fit, in combination with the user-friendly software from TSS. Along with the integration with GAC warehouse management system, several manual procedures were automated and digitized. And rather than sending shipment reports back and forth for investigation, automated notifications were implemented to alert the relevant team about any temperature excursions.
Elevating the temperature-sensitive logistics perspective
Implementing new technical platforms and work procedures are significant investments formost organizations. To justify the resources consumed in the process, the output needs to demonstrate a valid return on investment with either improved quality, lower cost, or higher efficiency.
For GSK and GAC, the results were positive right from the start. The solutions from TSS provided not only better quality with a more reliable platform, but also reduced costs and the time spent on manual administration. As a bonus, they realized the solution was more sustainable with recyclable loggers and fewer wasted expensive shipments.
A. Time and cost-effective
The implementation of solutions from TSS provided a lower Total Cost of Ownership (TCO) by optimizing process efficiency. Also, since it could be configured by the user to fit specific temperature profiles, there was no need to forecast shipments and keep a large stock of pre-configured hardware. One type of logger fits all shipment requirements.
“The people in my team are very comfortable with the TSS loggers. We find them very easy to handle. With other software platforms, where we often need to manually download data and send it to the supplier, shipments can often get quarantined for a longer time due to communication lead times. Reducing the manual tasks and automating the report distribution with TSS solutions saves us often more than 50% of the time,” said Mr. Mahesh Chandra Panchal, QA Supervisor at Mohamed N. Al-Hajery & Sons (One of the GSK receiving sites in the region).
Reducing the manual tasks and automating the report distribution with TSS solutions saves us often more than 50% of the time.
Most manual work and correspondence were removed by implementing seamless data flow through integration. This did not only result in less time spent on administration but also shortened the evaluation time to release shipments.
"I don't need to manually inform suppliers if there's an alarm because it's automatically sent to them. So, even when I'm not there, and someone else receives the logger, I can trust that the system does the work for me. It's really helped our business, so I give this logger a 10/10 score," said Mr. Mubeen Momin, Quality Control at Safwan Trading in Kuwait.
B. Quality beyond expectations
The new solution resulted in less manual administration and fewer errors in the processes. Instead of manually analyzing the data after shipments, the system did all the work, based on the temperature profiles pre-set in the shipments. Also, the automatic proof of delivery when the logger data was uploaded provided peace of mind to the teams.
"This platform is one of the most user-friendly I've seen, and I handle almost 100 temperature loggers from different distributors on a daily basis. You just plug it in, and the portal automatically informs me if there's an alarm. Compared to other systems, I spend very little time on the TSS solution, and it's been a huge help," added Mr. Mubeen Momin.
Compared to other systems, I spend very little time on the TSS solution.
The system managed all required analysis and communication, with no further effort fromt he users. Whenever a user was running an audit, or needed to access a report, the data was securely stored in a central and fully traceable repository.
C. Comprehensive service and 360°support
The close collaboration with account managers and specialists from TSS was well appreciated by the teams at GSK and GAC.
“TSS really makes my life easier. Not only because the system is good, but if we ever have a problem, the TSS Account Managers and Customer Services are always there for us,” explained Srilal Laurence, Contract Manager at GAC Logistics in Dubai.
In addition to the positive results with quality and resources, GSK and GAC discovered that their team’s wellbeing improved when the stress and time-consuming administration was removed.
After implementing the solution from TSS, the team is less worried.
"The number of issues related to distribution, which used to worry my team, was reduced and the time spent resolving issues was shortened. The wellbeing of my team is very important to me, and after we implemented the solution from TSS, they are less worried," said Mr. Ahmed Accoush.
D. Environmentally friendly
Another benefit of the new solution was sustainability. The recyclable loggers from TSS provided a low carbon footprint, and with more reliable data and automated analysis, fewer shipments of pharmaceuticals risk getting wasted unnecessarily. This is not only sustainable for the planet but also for the patients who receive their valuable drugs timely and safely.
Do you also want to investigate the opportunities for you to save time, cost and head-ache in your supply chain?
CONTACT us today to learn more about automation ≫